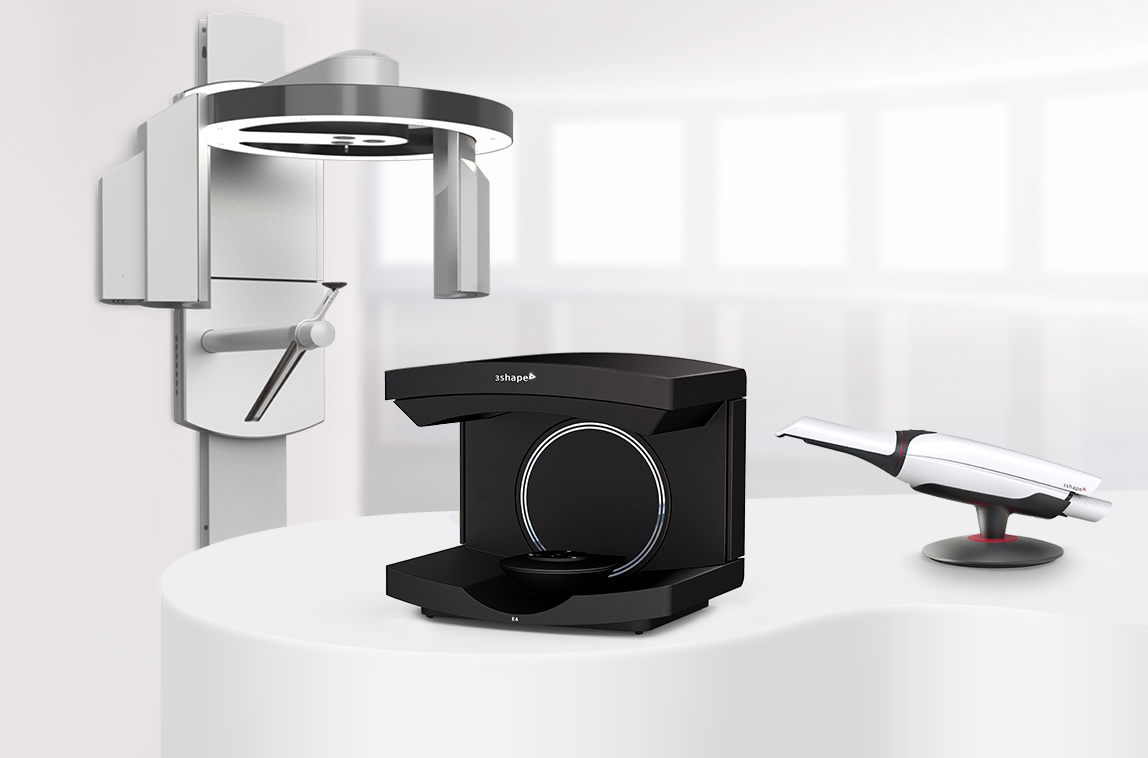
Even as recently as a few years ago, the dental implant process was a multi-step and time-consuming process. It often involved third-party laboratories and manufacturing facilities as well as a lengthy waiting period between initial temporary implants and the final prosthetics.
However, times are changing in cosmetic dentistry.
A new and exciting digital technological revolution is here. The old analog process is now giving way to a highly sophisticated digital process that is changing dentistry. The new digital revolution is excellent news for both patients and dental professionals alike.
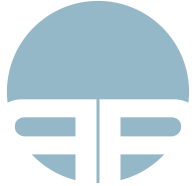
"The new digital revolution is excellent news for both patients and dental professionals alike."
DR. KAMRAN HAGHIGHAT, B.D.S., M.S., P.C.
Implant Digital Workflow
Before the recent introduction of a fully digital implant workflow, patients and doctors alike were consigned to a time-consuming, not user-friendly, and expensive process.
The old process of implementing a conventional dental implant procedure always began by taking an analog impression of a patient's mouth and the existing oral conditions. It was a time consuming and uncomfortable process that consisted of having patients bite down on a gooey or pliable substance to create a physical impression. Physical impressions are not always the most accurate way to model a patient’s existing bite. Slight shifts in the material, or in the way the patient happened to bite down on the gooey substance often translated into mistakes not known until much later that required more time and additional treatments to correct. Furthermore, the process of taking impressions is an uncomfortable process for patients and dental staff.
Once a physical impression was taken, the mold would be sent to a third-party manufacturer to create a prosthetic based on the impression obtained. The prosthesis was made and returned to the dentist several weeks later.
This period of dental implant limbo could be quite troublesome for patients who must cope with limited functionality and for doctors who must work with an ill-fitting placeholder. This implant process required patients to make multiple appointments to accommodate the time necessary to take and create dental impressions, send molds to an outside laboratory, craft a custom prosthetics, receive the final unit, and then fit it in place. This doesn’t even take into account the possibility of the final prosthetic failing a final test fit.
The new process is significantly more streamlined, faster, and accommodating for both patients and doctors alike.
New Dental Technology: A One-Two Punch
Accurate (and super fast) digital scanning, instead of physical mold-making, and real-time fabrication of essential prosthetic components, such as custom crown restorations, are game changers in dentistry.
With the introduction of rapid, real-time digital technologies, a significant portion of the dental implant digital workflow can now be cut in half.
Intraoral Scanners: Ultimate Productivity & Faster Scanning
Impressions can now be obtained more accurately, quickly, and comfortably using new scanning technologies such as the 3Shape TRIOS intraoral scanner which we use at Portland Perio Implant Center. This scanner eliminates the need for the "old" gooey physical impression process.
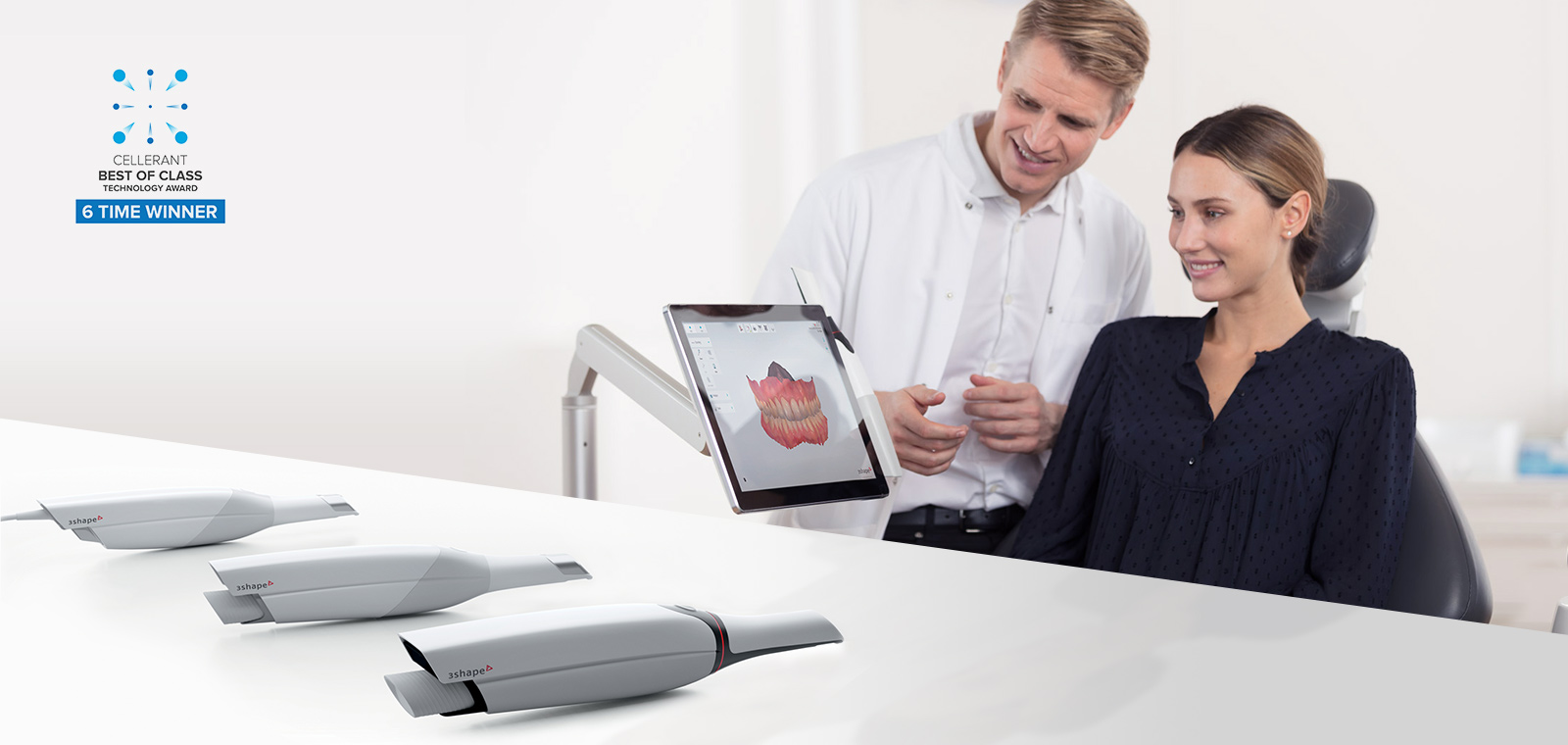
10 Benefits of Digital Scanning Process
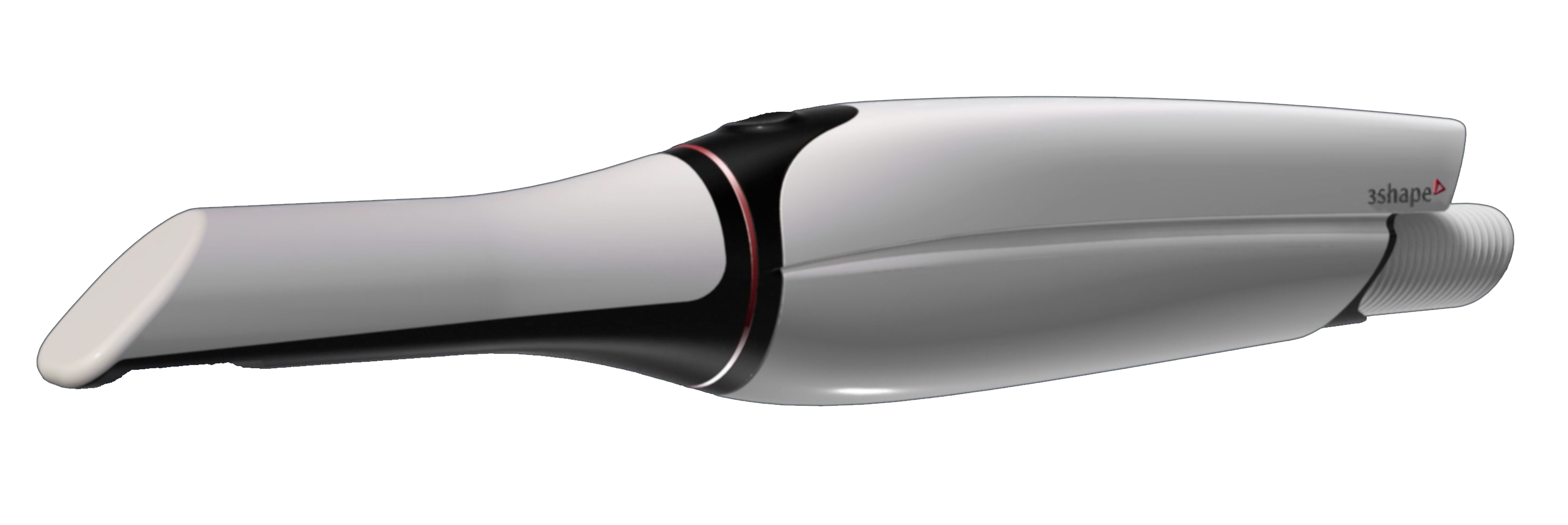
1. Scanning is easier and faster
Scanning is easier and faster due to the latest in Artificial Intelligence (AI) technology that removes unnecessary soft tissues as we scan.
2. In-house production
In-house production with the patient in the chair.
3. Dynamic occlusion
To perfect the restoration process TRIOS Patient-Specific Motion lets us record a series of different bite positions and highlight occlusal contacts for dynamic patient specific articulation.
4. Goes beyond scanning
Goes beyond scanning enabling preventative care with caries diagnostics aid and monitoring tools.
5. Creates a high-quality digital impression
Creates a high-quality digital impression in lifelike colors and we can apply shade measurement to evaluate treatment and activate quality dialogue with our patients.
6. Excites patients
Excites patients with Smile Design and Treatment Simulator
7. Seamless integration
Seamlessly integrates scanning, planning, and designing with 3D printers.
8. A modeless digital workflow
A modeless digital workflow for immediate implant placement and restoration.
9. Increased productivity
Increased productivity due to digital workflows which replace tedious manual tasks.
10. Exceeds patient's expections
Exceeds patient's expectations and satisfaction.
The move to digital scanning and real-time fabrication of prosthetic components has ushered in a revolution in the dental field.
3D Printing: The Catalyst for Digital Dentistry
The advent of 3D printing and other real-time printing innovations have moved the manufacturing laboratory into dental clinics themselves. Machines that in the recent past would have had their very own housing facilities can now be installed right in a dentist’s office, just like what we have done at Portland Perio Implant Center. We recently introduced the latest in 3D printing technology to our patients with Formlabs 3D printer which allows us to craft precise custom prosthetics for patients while they are sitting in the chair.

5 Benefits Realized From Our New 3D Printing Capabilities
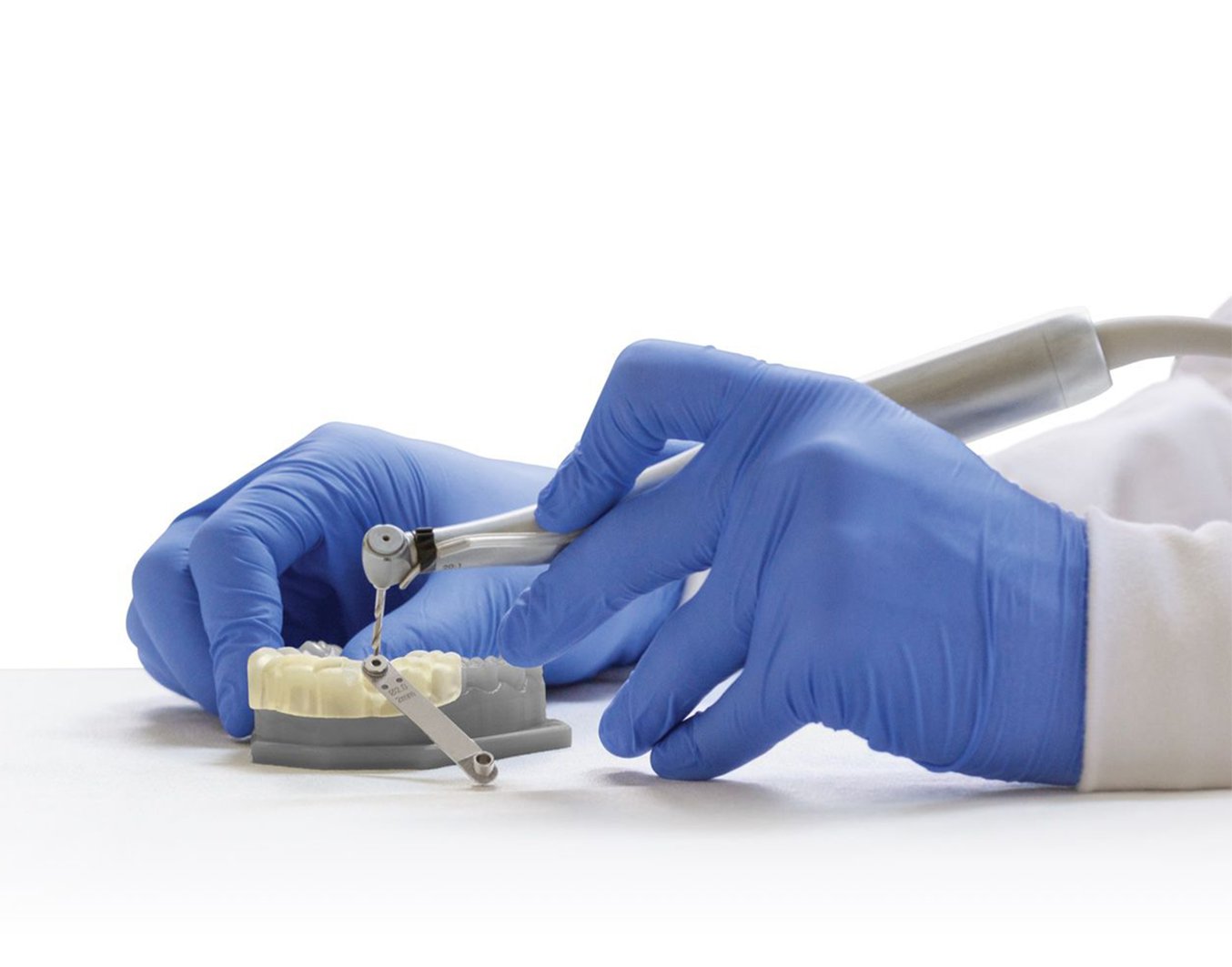
High precision 3D printing
Streamlined digital workflows that save time and money.
Professional precision
Accuracy tolerances for margin lines and die surfaces as tight as +/-35 microns on Dental Model Resin.
Integration with our intraoral scanner and CAD software.
Provides multiple applications
Applications from crown and bridges, clear aligner models, surgical guides, splints and occlusal guards, full dentures, and orthodontic models for wire Hawley retainers which improve efficiency and reduce turnaround time.
The New Dental Digital Implant Workflow
The new dental digital implant workflow begins with an accurate and fast scan that involves little to no patient preparation. Our cutting edge digital scanner utilizes the latest advances in artificial intelligence (AI), is statistically more accurate than conventional impressions, can image dynamic occlusion, and can even reproduce realistic colors.
Next, the scanning data is imported into a digital Computer Aided Design (CAD) software where real-time 3d modeling and manipulation can occur. This is often referred to as the modeling or design phase. Dental prosthetics are manipulated in real-time 3D restorations, shaped, positioned, and finalized. This takes all the guesswork out of the process and guarantees a high degree of accuracy.
When the 3D model is complete, it’s time to bring the digital product into the real world through highly advanced, commercial 3D printing technology designed specifically for the dental industry. 3D data is imported into a 3D printer which “prints” a real world, custom, prosthetic component from the ground up. These cutting edge printers such as Formlabs 3D printers have tolerances as small as approximately 35 microns when printing with dental grade resin. To put that in perspective, there are 25400 microns in a single imperial inch.
Finally, the printed component is “finished.” This involves washing, drying, post-curing, and touching up the final prosthetic form.
Once the finishing touches are complete, the newly crafted replacement tooth can be fitted intraorally.
This entire process can take place while the patient is sitting in the dentist’s chair.
Planning for dental implant therapy using cone beam and intraoral scans to fabricate and 3D print surgical guides in-house for precise implant placement.
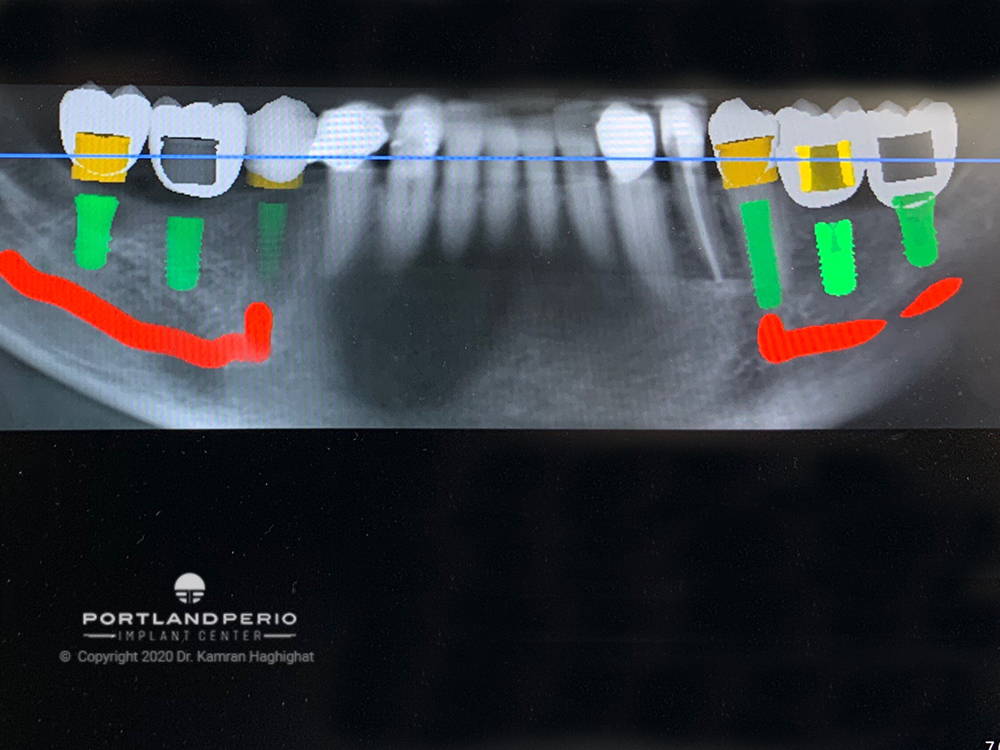
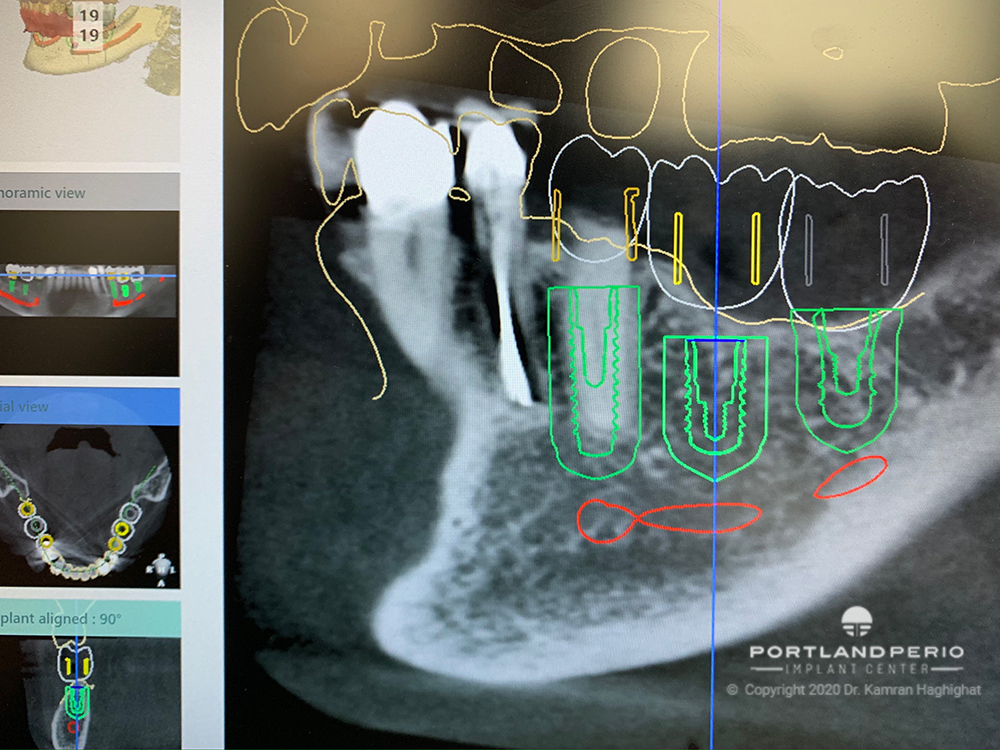
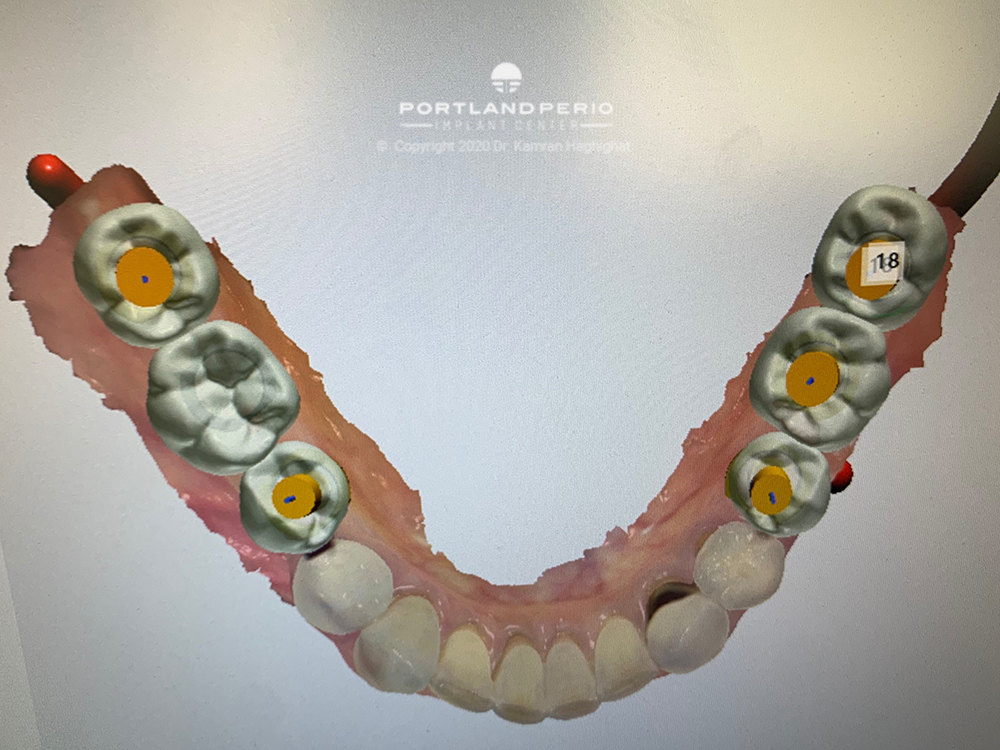
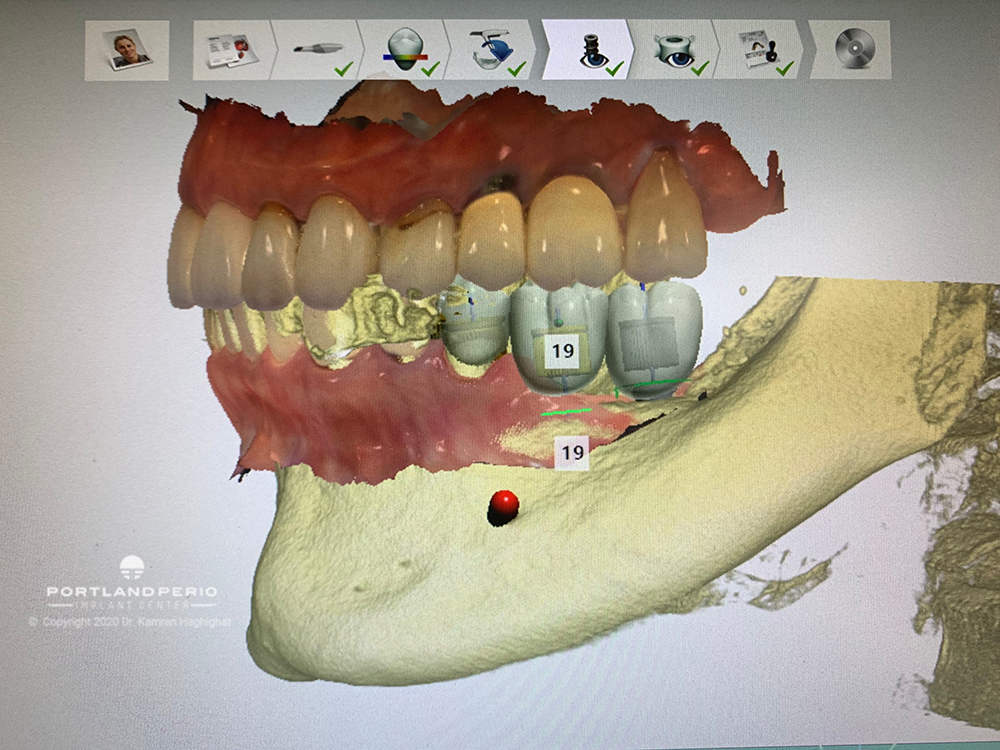
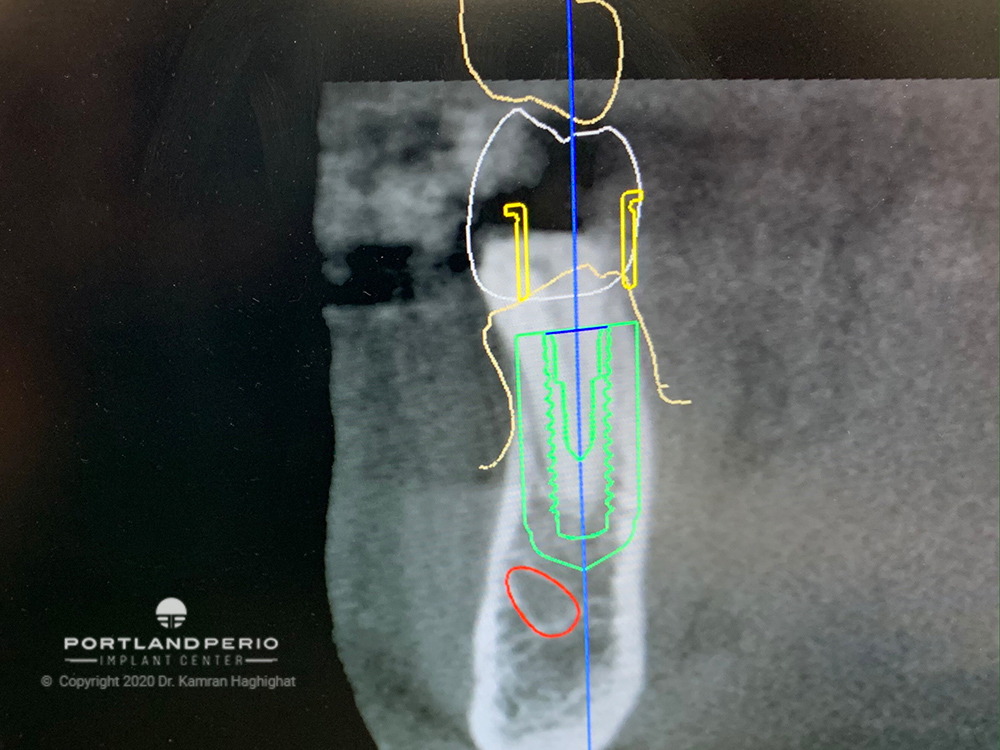
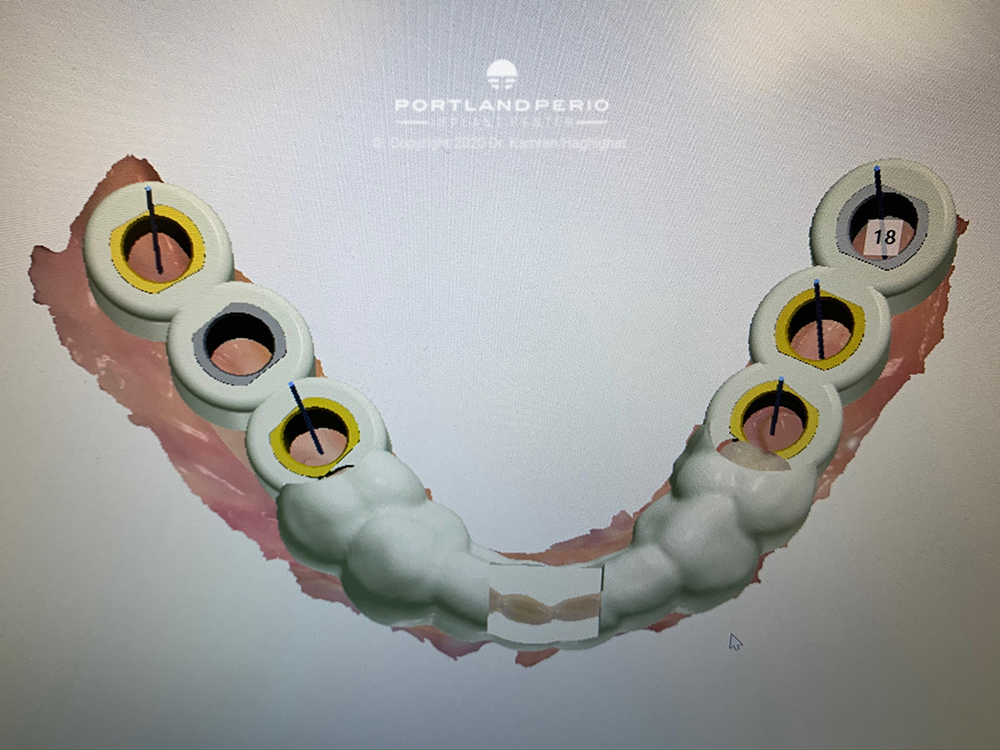
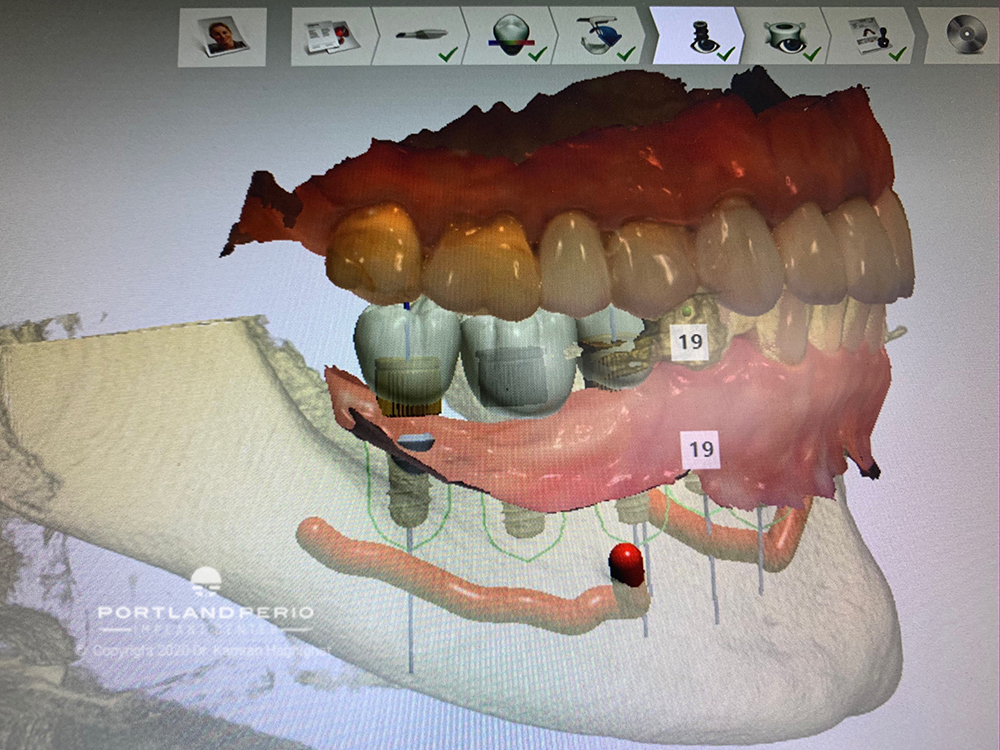
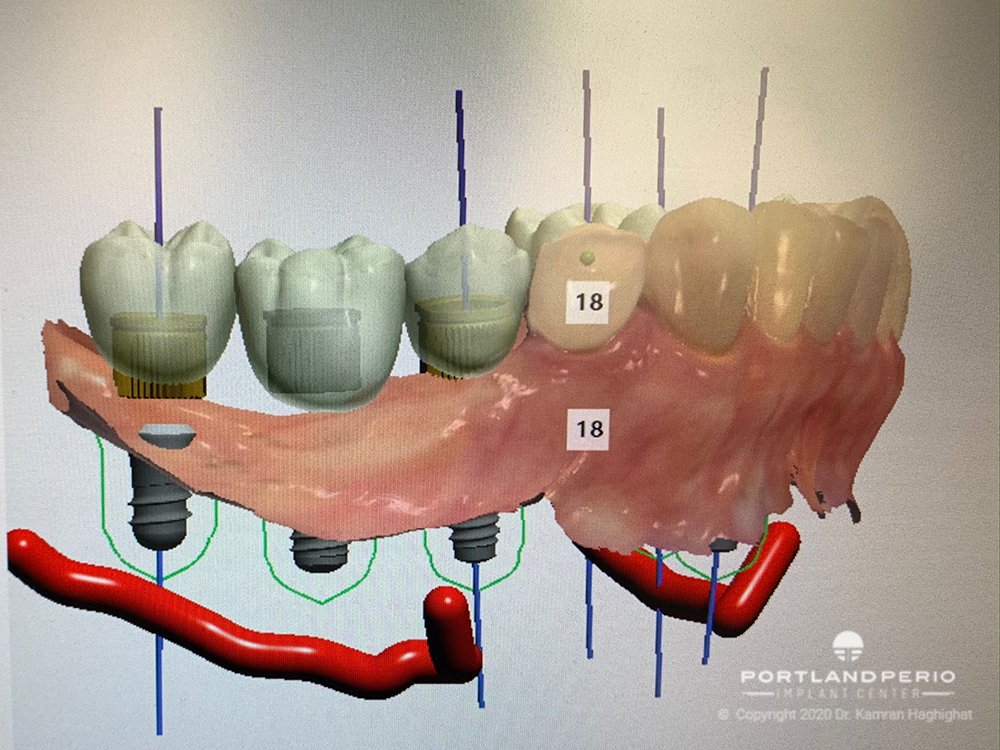
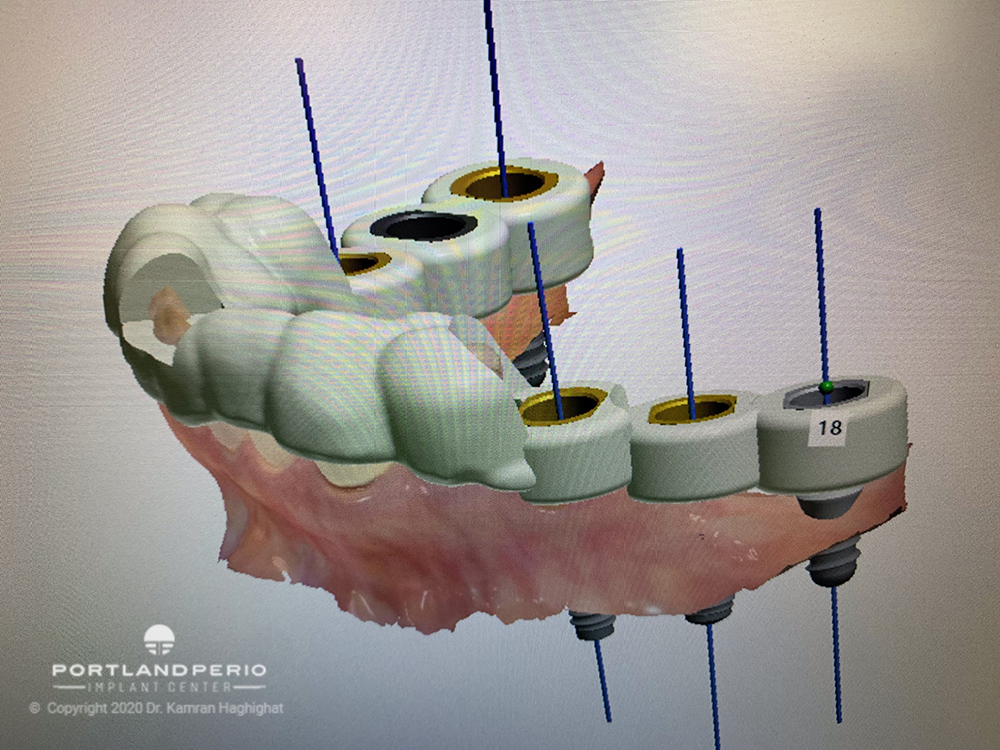
The Biggest Benefits from Digitizing the Dental Implant Process
No more "Goo"
No more dental impressions and uncomfortable dental trays filled with “goo.”
Accuracy & Fit
Digital scans are more accurate, more comfortable, and take a matter of seconds to complete.
Real-time Fabrication
Real-time fabrication means patients can often have they're final prosthetic fitted on the same day as their implant procedure.
Rapid-prototyping
Rapid-prototyping also means that new custom prosthetics can be quickly crafted on demand.
Efficiency
Dramatically reduces the timeline from start to finish.
Full digitization
Full digitization of the creation process means less waiting for patients and same-day delivery of finished, final dental implants.
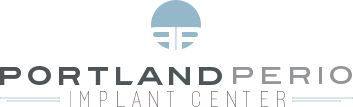
Dr. Kamran Haghighat uses the 3Shape TRIOS Intraoral Scanner as it is the industry leader in digital intraoral scanners.
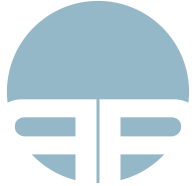
"Portland dentists, this is what we can do for your patients."
DR. KAMRAN HAGHIGHAT, B.D.S., M.S., P.C.